Recent
Predictive Maintenance Learning Center
Top Manufacturing Stories of 2024
Best Manufacturing Guides of 2024
What Is an Industrial PC?
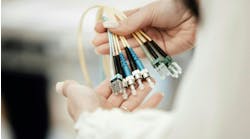
Electrochemical machining is gaining traction as an option for producing parts with hard-to-process materials and high-precision geometries. Having addressed the fundamentals and comparative advantages of ECM and pulsed electrochemical machining (PECM), it’s important to review how and where to apply these emerging manufacturing techniques.
ECM can often be the right process if the application matches at least one of the following criteria:
Volumes of Parts, not Prototypes
Each application calls for custom tooling, fixturing, and process parameters, which must be individually developed, which leads to higher up-front costs that are not suitable for prototyping projects.
ECM may not be cost-effective for prototyping, but its long-lasting tool life and fast removal rates make it particularly applicable for projects requiring thousands (if not millions) of identical parts or features on a single part.
Intricate Geometries
Electrochemical machining and pulsed electrochemical machining (PECM) can produce small, thin-walled, or complex-curvature features with relative ease due to the non-thermal nature of the process. In contrast, if you want to create a large flat surface or a tight OD diameter, for example, ECM is not a good fit.
Difficult Materials
ECM is not sensitive to mechanical properties and can machine a nickel super-alloy or hardened tool steel as easily and as quickly as it can process aluminum. Although ECM is routinely applied to challenging geometries in copper or aluminum, the value of ECM can be higher when the material is particularly unique or difficult to process.
Although numerous industries have parts that meet the above criteria, aerospace or medical applications are instructive examples of how ECM can benefit specific parts.
Aerospace Components
Aerospace manufacturing is guided by the need for extreme performance and low failure tolerance. Components must be light and withstand high temperatures, cannot fail unpredictably, and often have reasonable volume requirements whereby cost becomes a factor in the choice of the production process.
Aerospace machinists may need to work with particularly difficult metals—alloys that can withstand extreme temperature fluctuation, stress, and meet the minimum weight standards. All of these factors affect the integrity and performance of the aircraft.
Turbomachinery components—like compressor or turbine blades—not only adopt these tough materials but have airfoil tolerances of .002 in./.050 mm and surface finish requirements of 10 μin / 0.25 μm Ra. ECM and PECM provide value to such an application because they are unaffected by the material type—nickel superalloys or titanium aluminides are no problem—and the superior surface finish is achieved directly in the process with finishing passes or secondary operations.
The ECM tooling for this application is not simple and requires time and expertise, but once it is developed it can be significantly faster than machining operations and has led to adoption by many jet engine manufacturers.
Heat exchangers are another illustrative example. In terrestrial applications, an inefficient heat exchanger can be made heavy or large to provide the necessary performance. But, in aerospace machining or other specialty applications, the heat exchange may take place in a jet or rocket engine, requiring tough alloys that can withstand temperature fluctuations up to thousands of degrees, all while being as lightweight and compact as possible. ECM and PECM are capable of creating high feature-density with walls as thin as 50 μm—this enables efficient heat exchange and a smaller, lighter package, reducing the burden on additional subsystems.
Lastly, aerospace applications are safety-critical and can be particularly sensitive to fatigue life-failure issues (especially in commercial aviation.) Electrical discharge machining, for example, is known to produce a re-cast layer and heat-affected zone that can lead to crack propagation. In these applications, aerospace manufactures may specify an ECM process to avoid this issue, creating a surface with high-quality metallurgy.
Medical and Surgical Devices
The medical sector is in a constant state of innovation to deliver products that contribute to better patient outcomes while also reducing costs—the cost of both the device and the entire procedure. Surgical procedures that are less invasive and materials with better biocompatibility or performance all require manufacturing innovation.
Guided or robotic surgery can be performed with small surgical tools, a product category in which ECM stands out. Many of these materials are stainless steel alloys, and ECM delivers low-roughness surfaces that will impede bacterial growth and ensure more consistent operation by the device. In many cases, these surgical tools also are disposable, and the possibility to process multiple parts in parallel makes ECM and PECM an affordable production option. The surface finish and form quality tolerance also can be advantageous for the sliding components in orthopedic implants, achieving low surface-roughness on hard-to-reach 3D features, without resorting to grinding, lapping, or hand polishing.
Nitinol (a nickel-titanium alloy) is a common material for the manufacturing of medical devices. Its unique shape memory, elasticity, and biocompatibility make it an excellent candidate for a variety of applications in the medical sector, such as surgical sutures, orthopedic implants, and self-expanding stents. Some of Nitinol’s notable properties contribute to its difficulties, however. The material’s superelasticity makes it particularly difficult to machine. However, with ECM, the hardness, elasticity, or any other physical properties of the metal are irrelevant.
For some Nitinol applications, ECM can be used to produce implants without chip recutting areas and 3D-conforming surfaces that reduce irritation in the body. Or, for producing stent devices, the lack of burrs or heat-affected zones can eliminate a post-processing step. Some medical imaging technologies may require parts such as anodes and holders composed of refractory metals, such as molybdenum, rhenium, and tungsten. While these are excellent, heat-resistant materials, those qualities also pose complications, as they are particularly difficult to machine.
Historically, ECM has not been a good solution for processing refractory metals due to their oxide layer but recent advances in the technology are changing this paradigm, allowing ECM to create the necessary refractory metal parts for medical imaging applications.
Supplementing Metal Additive Manufacturing
Electrochemical machining also can support additive manufacturing, or 3D printing so long as the material being printed is a conductive metal. Many high-value applications in aerospace and medical devices are being assigned to metal AM operations, and ECM can play a complementary role to those processes. The manufacturers may opt to use 3D printing for projects that require delicate geometries (even jobs that ECM is fit for, such as high-temp heat exchangers), but electrochemical machining can provide two benefits to this application—surface finish improvement and geometry creation.
Surface roughness is a common concern for metal AM parts, especially due to support structures production leaving behind remnants or irregularities appearing on downskin surfaces. These irregularities can promote microscopic cracks and create unnecessary friction that may impede the part’s utility and even cause damage.
ECM and PECM can alleviate these issues by intensively polishing surfaces in areas where a smooth finish would be important (e.g., orthopedic implant bearing surface), while leaving other areas in the original state (e.g., osteointegration features on a knee implant.)
Bulk finishing methods (vibratory, electropolishing, etc.) are inexpensive but are not selective without masking. In addition, those processes may not effectively remove large support structure remnants. In contrast, ECM and PECM use tool proximity to locally remove material, addressing both macro and micro surface roughness.
Using an ECM/PECM tool to finish metal AM parts also can be used for feature machining, not just surface finishing. ECM can create unique geometries and thin-walled structures with ease. While most additive manufacturing processes can achieve a minimum wall thickness of around 0.5 to 1 mm, ECM can produce features of <0.1 μm. For example, a 3D-printed nickel-alloy turbine component was post-processed by electrochemical machining to remove the downskin surface roughness while also achieving the thin edge quality required on the trailing edge.
As metal additive manufacturing continues its growth into higher volume applications, manufacturers are looking for the most cost-efficient techniques. By leveraging ECM, a manufacturer might 3D-print a metal part rapidly with poor surface finish or tolerances but apply ECM to create the critical features—resulting in a more efficient manufacturing process.
Expanding the Toolbox
Electrochemical machining and pulsed electrochemical machining are tools available to machine shops and other manufacturers now and can address applications in a variety of fields. Shops supplying the automotive industry may use ECM to process fuel injectors and components of automatic braking systems. The robotics industry can use it to produce precision gear components for robotic joints. Producers of electronics enclosures may use PECM to create discrete, thin-walled features with accurate depth control, for mounting components. No matter your industrial sector, if you have components that may benefit from the features available with ECM or PECM, consider this process capability during your next design review or manufacturing planning meeting.
In part three of this series, we will explore more potential usages of ECM and how it can play a role in the industry of the future.
Also see the first installment, A Guide To Electrochemical Machining: Part 1.
Kirk Gino Abolafia is the Technical Marketing Manager for Voxel Innovations, Inc., Raleigh, N.C.